Premium Snack Producer Case Study
“The quickest payback of any project our Company has ever done.”.
Project Manager
The Customer: UK Snack producer
Country: UK
Industry: Snack Industry
The Challenge
- To reduce the cleaning time between flavour changes
- To increase productivity.
- To improve hygiene.
The Solution
- An in depth assessment of clients’ requirements.
- Bespoke rack and washing machine to wash chutes and weigh heads simultaneously.
- Full project management delivering seamless transition from design to installation.
The Offering
- Design, supply and installation of two Rack Hydro washing machines on a mezzanine level.
- Operation and maintenance training to ensure maximum efficiency and longevity of the machines.
- Planned and reactive maintenance service.
- Full detergent package including a dosing system, chemical supply and regular inspection visits.
The Benefit
- Cleaning process time reduced from 109 minutes to 60 minutes per weigh head set
- An additional 35 hours of production per week
- Installation payback completed in 8 weeks.
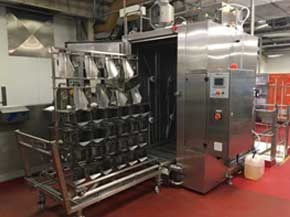
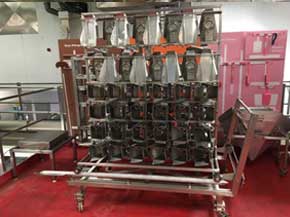
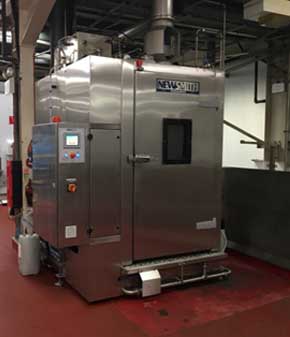
A recent Newsmith installation has been hailed as the fastest payback project that the UK premium crisp producer has ever commissioned.
Paul Careless, Sales Manager at Newmsith Stainless, worked closely with the customer on the design of the machine to maximize operational efficiency.
The installation of a Rack Hydro wash and rinse machine has seen the manual cleaning process time reduced from 109 minutes to 60 minutes per weigh head set. In a crisp production facility where the cleaning process is undertaken every flavor change, an additional 35 hours of production time per week, previously lost in cleaning, has been realised.
Prior to the automation of the washing process, chutes and weigh heads were removed for washing, transferred onto trolleys and wheeled to the wash bay. Weigh heads were transferred from the trolleys to a cabinet washing machine. However, chutes were too big and had to be washed manually in sinks. After washing everything was transferred back onto trolleys and back to production for refitting.